How Manufacturing Data Analytics Can Improve Productivity
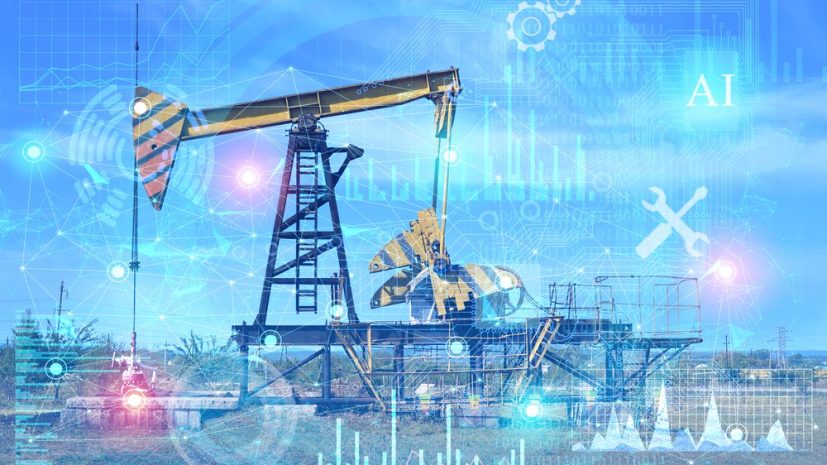
Posted: March 19, 2024
The oil and gas industry is fiercely competitive as companies vie for both finite resources and market dominance. Efficiency and innovation are key to improving production, reducing operational costs, and minimizing the environmental impact. Much like other sectors, advancements in technology and automation are continuing to transform the oil and gas industry. Data analytics monitors operations and safety in real time.
This quest for improvement doesn’t only propel profitability. It’s also essential to meet stringent regulations and evolving energy demands in a rapidly changing landscape. In this article, we explore how technology in the oil and gas industry drives purchasing power and how data analytics boosts productivity.
The Role of Data Analytics in the Manufacturing Sector of the Oil and Gas Industry
Data analytics is a transformative force in the oil and gas industry. It drives efficiency and optimization at every stage.
Analytics helps companies identify operational efficiencies, from material sourcing through to goods receipt, as well as monitoring and managing energy consumption. It also classifies improvements to reduce costs and lower the carbon footprint. Using data analytics for sophisticated process control ensures that manufacturing processes remain within desired parameters to enhance efficiency and ensure product quality.

3 Data Analytics Strategies to Improve Productivity in Oil and Gas Manufacturing
With the following strategies, oil and gas operators can see significant gains in efficiency, cost savings, and productivity. They may also improve safety and environmental stewardship.
1. Optimize Supply Chain and Procurement
Efficient supply chain operations are critical in the oil and gas industry. Companies operate across widespread locations and often need to rapidly mobilize expensive, specialized materials and equipment to support well development and production.
Operators require a steady provision of components and materials to ensure ongoing maintenance and reliability for production. Data analytics in manufacturing operations provides an integral role in effective demand forecasting, inventory management, and supplier performance.
Demand Forecasting
Data analytics tools study patterns in consumer behavior to help companies anticipate changes in demand. By analyzing historical data, market trends, seasonal fluctuations, and economic indicators, predictive analytics can accurately forecast future demand for oil and gas products.
Inventory Management
The review and assessment of historical data can determine and provide a road map for just-in-time inventory practices, reducing holding costs and minimizing waste. Trend analysis recognizes patterns in inventory data. When these patterns are combined with projections based on historical data, operators can better align inventory levels with anticipated market demands.
In addition, enhanced algorithms determine the optimal stock levels, reorder points, and order quantities. This balances the costs of inventory holding against the risks of stockouts.
Supplier Performance
Performance metrics analysis tools track and evaluate key performance indicators (KPIs) for suppliers. This includes on-time delivery, quality of materials, and compliance with contracts. Companies also use analytics to assess the risks associated with each supplier. They consider factors like geopolitical issues, financial stability, and reliability to mitigate potential supply chain disruptions.
By sharing data with suppliers, both parties can gain insights into performance and work together to improve the supply chain. The integration of data analytics lets companies be more agile, responsive to market conditions, and efficient in their operations. They’re better able to predict and meet demand, manage inventories, and ensure that supplier relationships contribute positively to the bottom line.
Gilmore, for instance, runs largely on a forecast model. The model provides a strategic advantage in an unstable supply chain environment to ensure that our customers get the flow control products they need when they need them. We also implement an economical batch size strategy based on customer order cadence. Forecasts keep on-demand items in stock, and economical batch production ensures better pricing and availability for our customers.
2. Enhance Equipment and Asset Management
Equipment failures can disrupt production, significantly increase costs, and interrupt the entire supply chain. Data analytics is shifting the industry from reactive to proactive strategies. This leads to lower costs, improved safety, and higher efficiency.
With advanced analytics, the industry can predict potential equipment failures before they occur. Historical data from equipment sensors is analyzed to identify patterns and anomalies that precede a failure. By understanding how and why equipment fails, manufacturers can implement strategies to preempt these issues.
On a daily basis, under normal operating circumstances, devices and sensors continuously collect data on equipment status, environmental conditions, and production processes. Real-time analytics enable immediate adjustments to manufacturing operations, ensuring optimal performance and reducing unforeseen setbacks.
As a leader in flow control solutions, Gilmore leverages large datasets, including historical and real-time operational information, to foresee and prevent potential breakdowns. Predictive tools help to schedule maintenance tasks proactively and plan for replacements and upgrades promptly to minimize unnecessary downtime.
3. Advance Process Automation and Operational Efficiency
Real-time data enables manufacturers to monitor processes closely and make immediate adjustments to improve efficiency and output. This often occurs through automated systems that adjust parameters on the fly. Manufacturers can then optimize the use of materials, machinery, and labor, ensuring that resources are used effectively and reducing waste.
Analytics helps benchmark performance across different lines, shifts, or even plants, allowing for the identification and replication of best practices throughout the organization.
Data analytics can also improve quality control by detecting anomalies or deviations from the expected output. This ensures that any quality issues are identified and rectified promptly, reducing waste and rework.
By analyzing data from the supply chain, manufacturers can identify bottlenecks, fine-tune the demand outlook, and optimize inventory levels. This reduces working capital and ensures that production can respond quickly to industry changes.
Innovation Through Insights: Strengthening the Oil and Gas Sector
Integrating manufacturing data analytics into production processes fosters a culture of continuous improvement. This culture is crucial for the oil and gas industry to thrive amid market volatility and regulatory pressures. With data analytics, operators can significantly reduce operational costs, enhance production, improve safety, and ensure environmental compliance. The result is a more competitive and sustainable operation.
Gilmore has established itself as an industry innovator and leader in superior-quality flow control solutions. Our team of expert engineers prioritizes safety, operational efficiency, quality, and reliability while striving to offer the best pricing strategy.
Even better, our established distribution partner network supports global markets. Contact us to learn how we can help you reduce operational costs and improve productivity in your energy operation.